Опытное Конструкторское Бюро «Кристалл» берет свое начало еще с 40-х годов 20 века и неразрывно связано с развитием авиационной науки и техники в России.
Основное направление предприятия - разработка и производство агрегатов авиационных топливных, гидравлических и электрических систем. Одним из основных клиентов ОКБ «Кристалл» является «Корпорация «Иркут» - производящая пассажирские лайнеры Sukhoi Superjet и МС-21.
Руководитель производства Антон Александрович Юкиш рассказал об эффективном применении аддитивных технологий в авиационной промышленности.
Внедрение 3D-печати в современное производство
В качестве импортозамещения мы изготавливаем системы электроснабжения самолетов, системы кондиционирования, топливные системы, насосы для перекачки керосина и другие агрегаты входящие в самолеты. Раньше, Sukhoi Superjet состоял на 70% из импортных комплектующих, а в новой модификации лайнер Sukhoi Superjet New будет на 90% состоять из отечественных.
Конечно, для создания подобных агрегатов используются традиционные методы изготовления, но без аддитивных технологий в нашем производстве не обойтись. Пять месяцев назад мы запустили целую 3D-ферму, состоящую из 15 принтеров Raise3D Pro3 и Pro3 Plus для 3D-печати транспортировочных заглушек и колб, подставок под агрегаты, корпусов для литья, приспособлений для сборки агрегатов и др.
Т.к. основная сборка самолетов находится в Иркутске, транспортировка должна быть очень надежная, пока агрегат доедет из Москвы до клиента. Таким образом наступила потребность в изготовлении пластиковых деталей способных защитить во время транспортировки агрегаты от повреждений.
Раньше мы изготавливали заглушки на токарных станках и ЧПУ. На токарных получалось очень долго, на ЧПУ быстрее, но загружаются дорогостоящие станки. Стоимость одного нашего станка с ЧПУ сейчас около 20 млн. рублей, нерентабельно изготавливать из пластика детали на таком дорогостоящем оборудовании. Поэтому выгоднее взять 10 принтеров на 6 млн. и производить тоже количество деталей, что и на ЧПУ за 20 млн.
Почему мы выбрали принтеры Raise3D
Перед покупкой мы, конечно, проработали ряд производителей и моделей 3D-принтеров, Raise3D выбрали как самый подходящий вариант по качеству, производительности и цене. Рассчитали, какое количество деталей в год мы будем печатать, и вышло, что под наши задачи 15 принтеров нам достаточно.
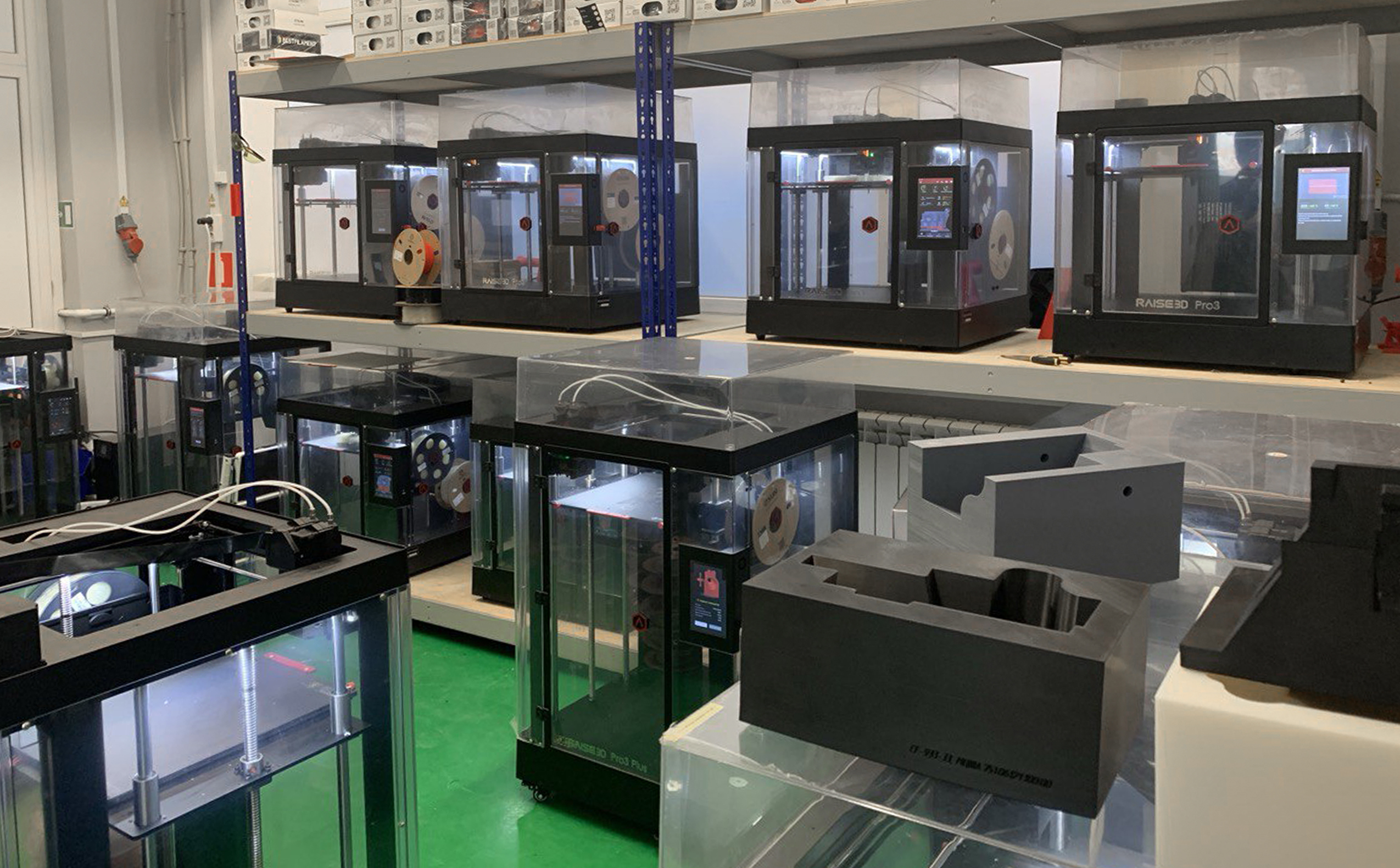
Освоить технологию 3D-печати было не сложно, у нас уже был опыт, мы печатали выжигаемые модели. А так как мы являемся конструкторским бюро и у нас огромный штат конструкторов, готовые модели для печати мы получаем от них.
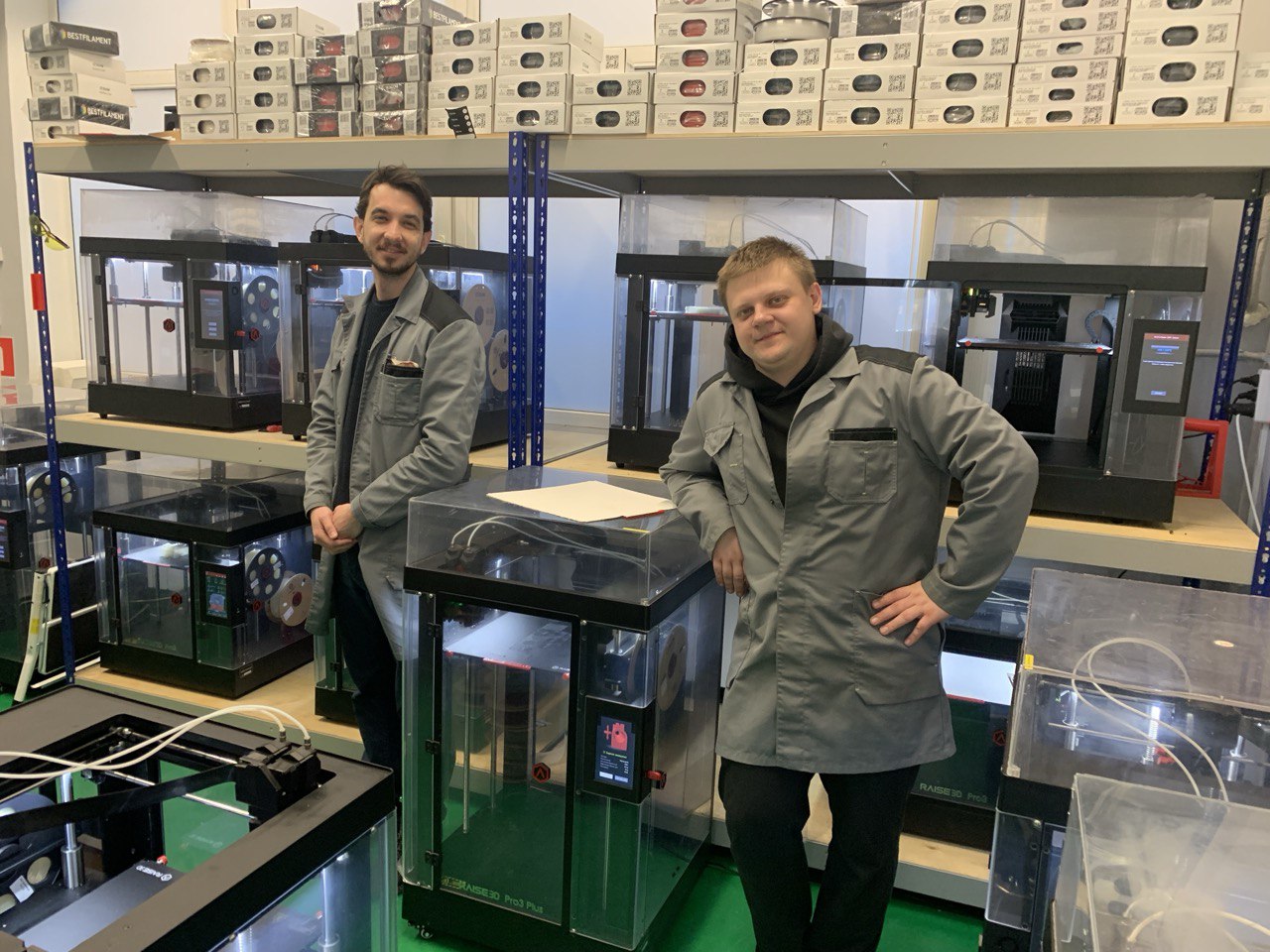
На самом деле, для работы с 3D-фермой из 15 принтеров большой штат не требуется, достаточно одного конструктора, двух операторов и одного инженера. В нашем случае, нам достаточно двух операторов. Наш ведущий оператор Кирилл Вичас с 10-ти летним опытом в 3D-печати совмещает функции оператора и инженера.
3D-печать 24/7
3D-принтеры печатают нон-стопом 24/7 с перерывом на снятие отпечатка со стола. Время печати зависит от модели, материала, процента заполняемости отпечатка, например корпуса для литья печатаются от 10 до 70 часов. Есть и такие модели, время печати которых доходит до 400 часов, и здесь важно не проморгать момент замены катушки, иначе печать прервется, межслоевая адгезия нарушится, и многочасовая работа пойдет насмарку.
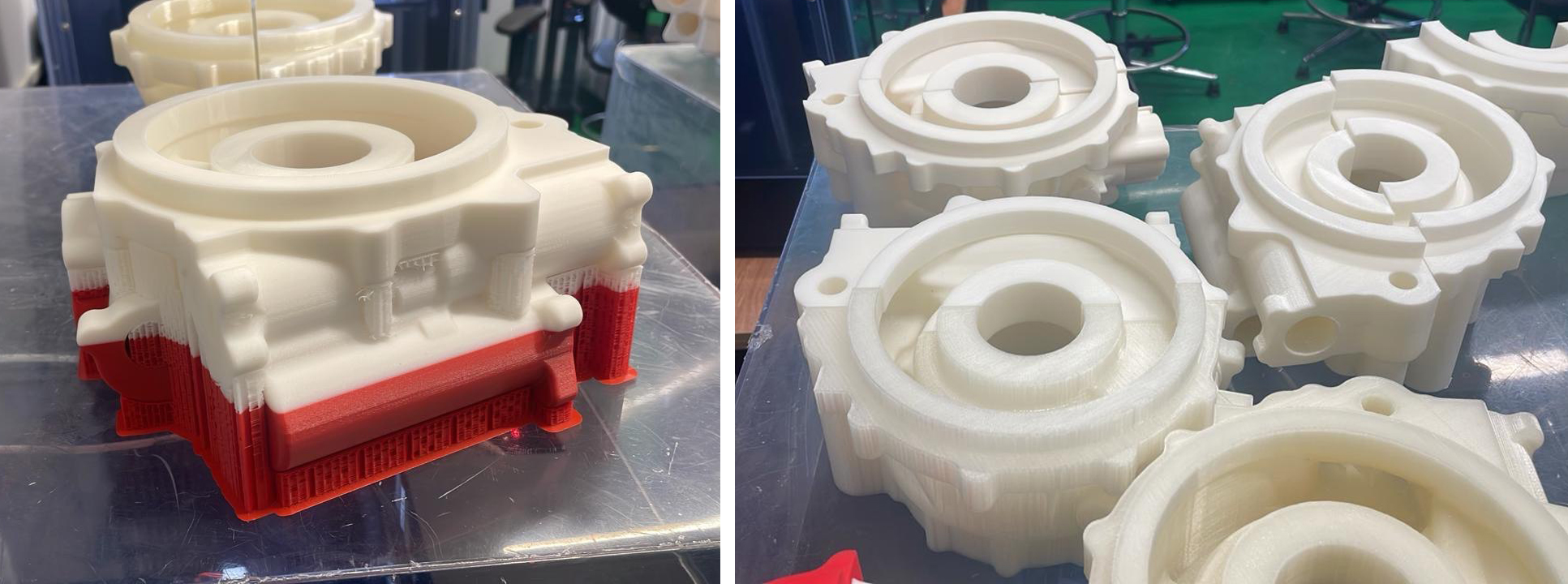
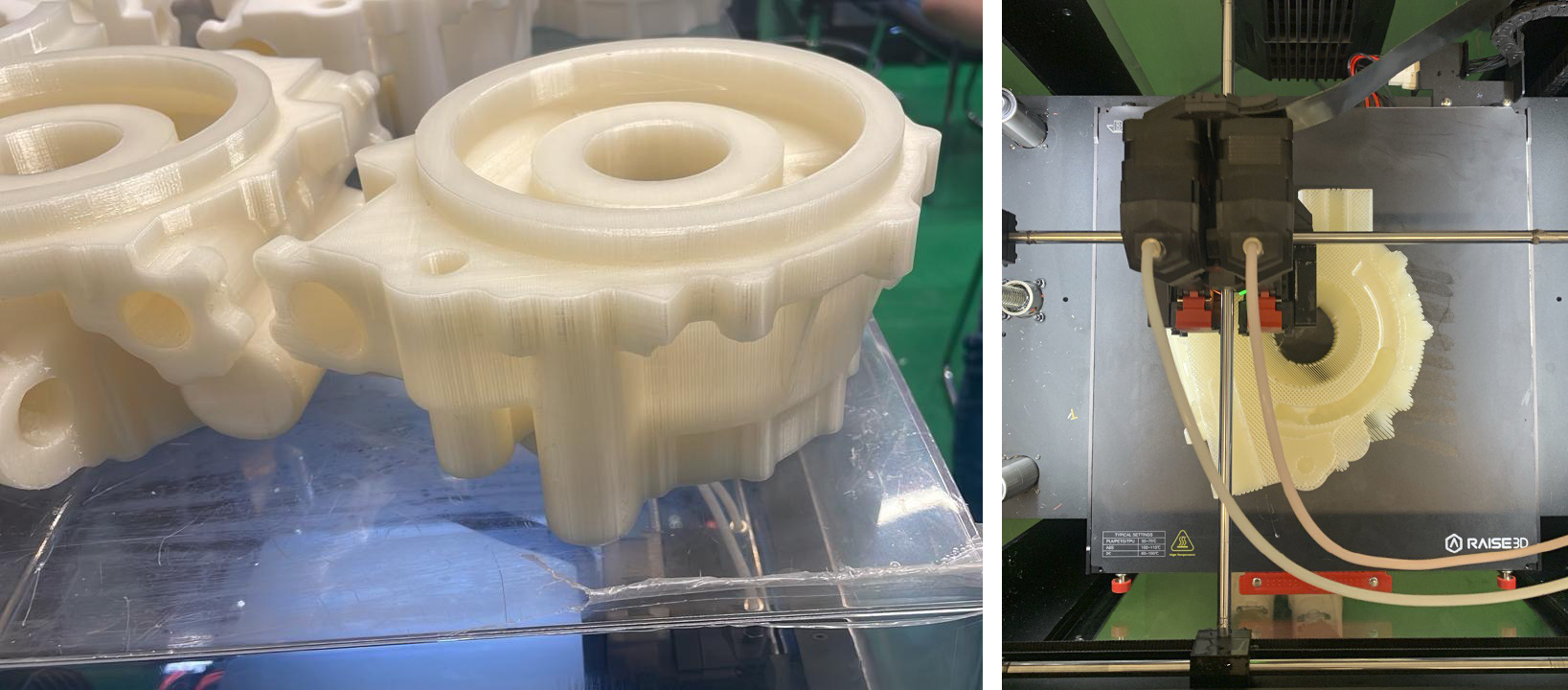
Корпусы для литья, напечатаны из PLA-пластика.
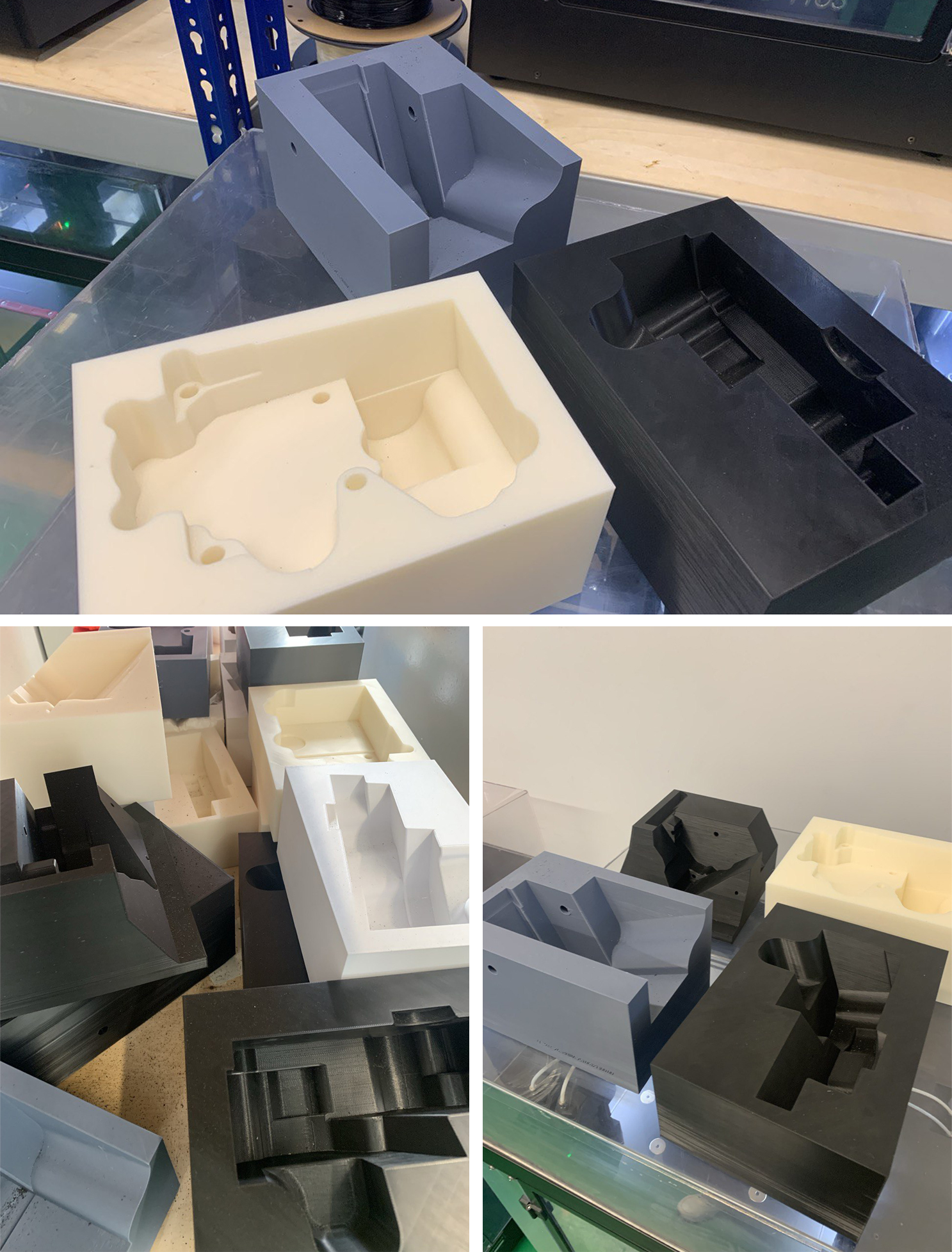
Подставки под агрегаты, напечатаны из ABS-пластика.
В нашем арсенале есть 3D-сканер, но мы не используем его для реверс-инжиниринга, мы пользуемся им для контроля качества напечатанных деталей. После печати мы сканируем деталь, смотрим какие у нее отклонения по геометрии, есть ли деформации, затем отбраковываем или работаем с ней дальше.
Самый ходовой материал у нас - это ABS, из него печатается большинство моделей.
Заглушки, напечатаны из ABS-пластика. Они защищают важные соединительные фланцы и все остальные части агрегата, которые могут повредиться при транспортировке.
PLA используем для выжигаемых моделей. Мы отработали технологию изготовления выжигаемых моделей из PLA на принтерах Raise3D. Сначала печатаем модель, потом собираем литниковую систему восковую, после пропитки крепим к ней заготовки из PLA, затем красим смесью электрокорунда и этилсиликата, ставим эту конструкцию в печь, PLA выгорает, остается только керамика.
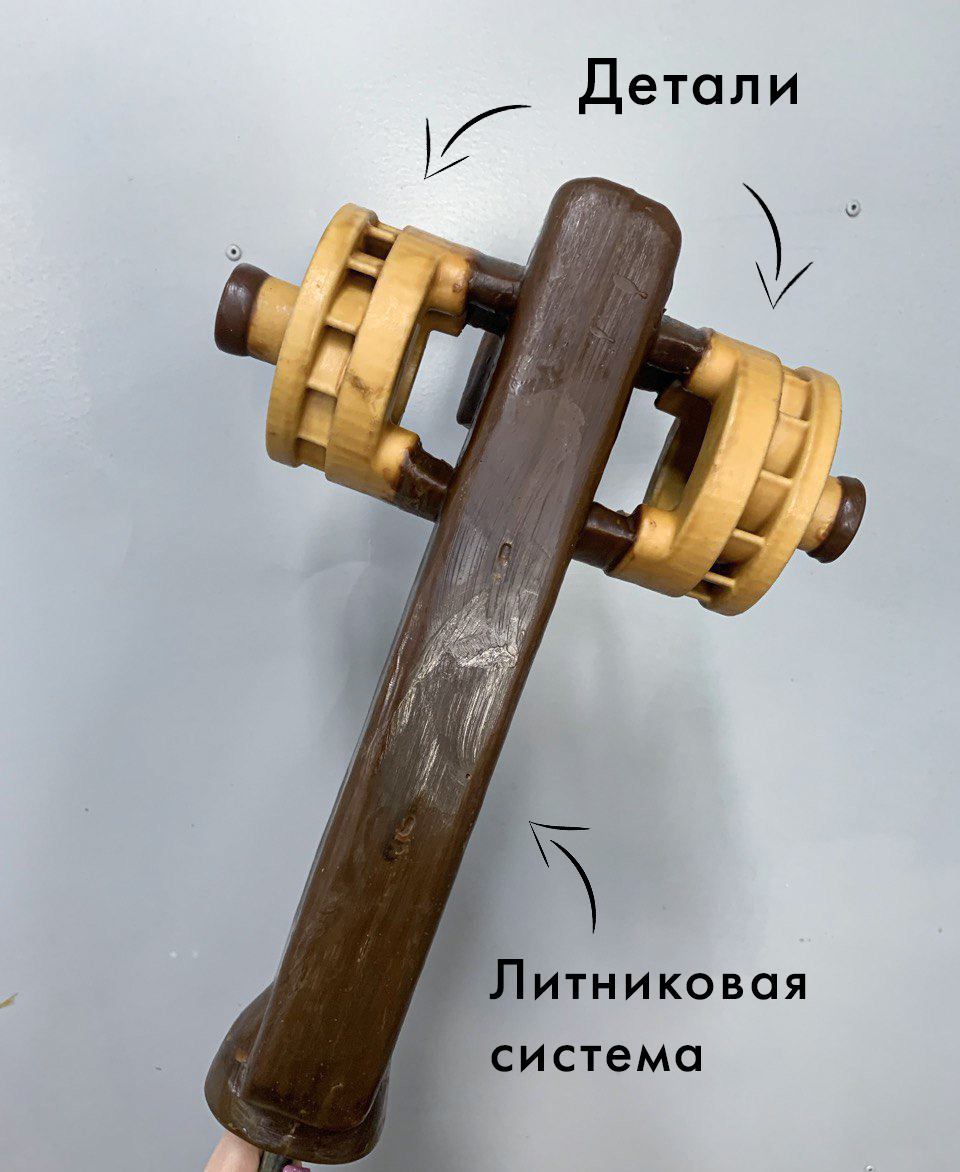
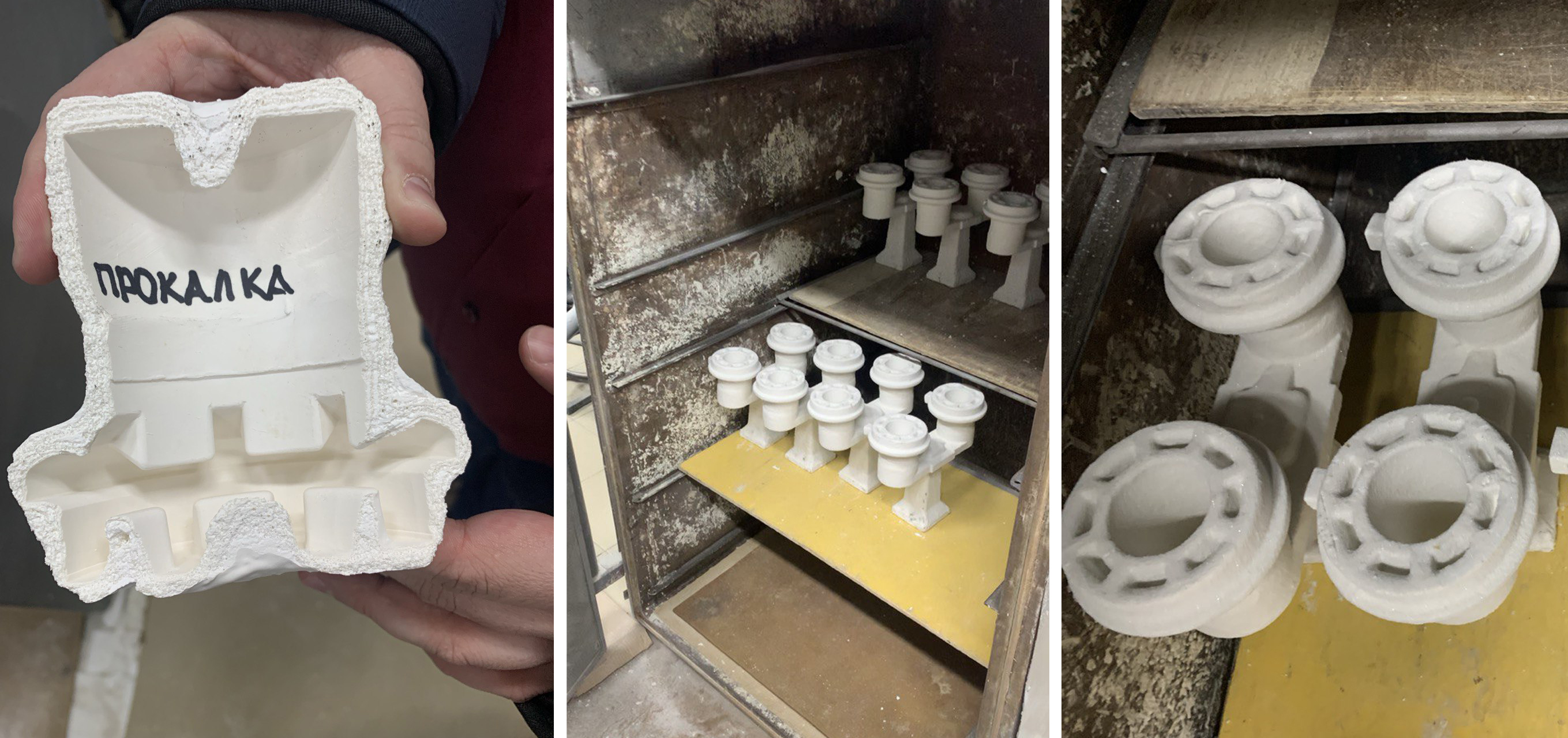
Готовая выжигаемая модель
Как рассказал Кирилл Вичас (инженер-оператор), - «За 5 месяцев мы испробовали печать такими материалами как PLA и ABS, в т.ч. наполненные, поликарбонат, полипропилен, полиамиды стеклонаполненные, карбононаполненные.
Самое сложное было печатать из полипропилена рамки для использования в гальванике. Этот материал более капризный, нужно было постараться, чтобы детали получались размер в размер.»
Рамки из полипропилена
«Принтеры Raise3D - одни из топовых настольных FDM-принтеров, они очень стабильны, и дают возможность печати широким спектром пластиков включая инженерные. Главное вовремя делать ТО и с ними не бывает проблем. Недостаток только в цене комплектующих,» - поделился Кирилл.
Будущие планы
«В планах у нас переход на полиэфиркетон PEEK, его механические свойства очень близки к алюминию, но он легче, и в отличие от алюминия им можно печатать. А в авиации большинство деталей делаются именно из него.
Сегодня этот процесс на этапе тестирования, и если все получится, то вместо литья будем переходить на PEEK. В этом случае наша 3D-ферма пополнится еще порядка 10-ю принтерами. И это сильно сэкономит наш бюджет и сократит время производства.
Сейчас некоторые детали мы делаем из прутка, используя ЧПУ-станки, которые в стружку переводят наши деньги. Мы закупаем дорогой пруток, а потом на дорогом станке его обрабатываем. Но помимо экономически выгодной перспективы использования PEEK, у нас получится снизить вес деталей, что для самолетов крайне важно!» – заключил Антон Юкиш.